
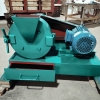
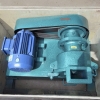
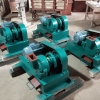
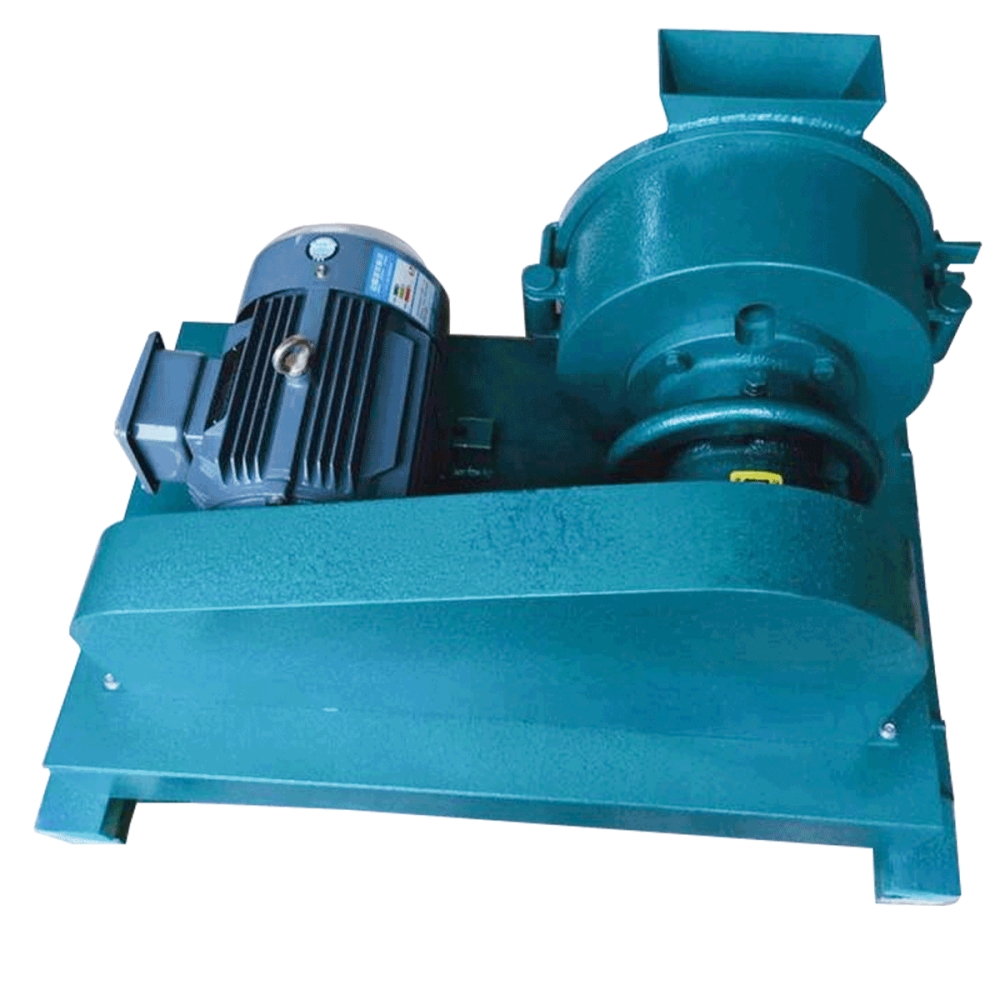
Laboratory Disc Pulverizer
Manufacturer : MORETEC
Part number :
OEM Compatibility :
Category :Laboratory
Description
Description
Laboratory disc mill (also known as disc mill or disc crusher) is a material crushing and pulverizing equipment designed for laboratory applications, suitable for grinding and pulverizing materials with medium hardness, brittleness and large particles. It achieves the crushing effect through the shearing force, squeezing force and friction force generated by the rotating disc, which is widely used in mineralogy, chemistry, environmental protection, building materials and other industries for material experimentation and analysis.
Main Features:
Working Principle:
The laboratory disk pulverizer consists of a pair of parallel rotating disks. The material is fed into the two discs through the inlet, and is gradually crushed by shearing, extrusion and friction between the two discs.
After crushing, the small particles will be discharged from the discharge port. You can adjust the gap between the discs to adjust the granularity of the crushed material.
Structural design:
Discs: usually made of wear-resistant alloy steel, carbide or ceramic materials to ensure wear resistance in long-term use.
Transmission system: the disc is driven to rotate by electric motor, and the driving method can be realized by belt, gear or direct drive.
Feeding and discharging port: The material enters the crushing chamber through the feeding port, and is discharged through the discharging port after crushing.
Adjustment mechanism: the gap between the discs can be adjusted to accurately control the granularity of the crushing.
Particle size adjustment:
Laboratory disk pulverizer can precisely adjust the granularity after crushing, applicable to different experimental needs. The coarseness and fineness of the particles can usually be controlled by adjusting the distance between the disks or adjusting the rotational speed.
Efficiency and fineness:
Disc Pulverizers are capable of providing high pulverizing efficiency and grinding to finer particle sizes. Common particle sizes typically range from a few microns to a few millimeters, depending on the nature of the material and the equipment setup.
Simple to operate and easy to clean:
Compared to some other complex pulverizing equipment, disc mills are simpler in structure and intuitive to operate. It is also easier to clean and maintain, making it especially suitable for laboratories that require frequent material changes.
Main Applications:
Mineralogical and metallurgical research:
Laboratory disc pulverizers are commonly used for preliminary crushing and grinding of ore samples, especially in mineral sorting, mineral analysis, and particle size control of ores.
Chemical & Pharmaceutical Industry:
Many chemical reactions or the synthesis of pharmaceuticals require fine crushing of raw materials, disc pulverizers are able to handle raw materials of different natures and meet the demand for high-precision particle size control.
Building Material Industry:
Used for crushing raw materials such as cement, gypsum, lime, construction sand, etc., especially in laboratory tests often need to grind different types of particles.
Environmental protection industry:
In the fields of solid waste treatment and waste recycling, disc pulverizers can efficiently crush and grind different types of waste and recycled materials for further processing and utilization.
Material Science and Powder Research:
Used for material powder research, especially experiments involving particle morphology, particle size distribution, and fluidity of materials.
Factors to consider when choosing a laboratory disk pulverizer:
Material Characteristics:
Different materials (e.g. ores, plastics, metals, etc.) may require different pulverizing equipment. Selection needs to ensure that the pulverizer is suitable to handle the hardness, toughness and moisture content of the target material.
Particle size control requirements:
If the experiment requires very fine granularity after crushing, you need to choose a wide range of adjustable particle size, high precision operation of the equipment.
Processing capacity and efficiency:
According to the actual needs of the laboratory to choose the right type of pulverizer, to ensure that the equipment can be in the right time to deal with enough material.
Equipment durability and maintenance costs:
The material of the equipment, wear resistance and the convenience of cleaning and maintenance are the key factors to consider when purchasing.
Brand and after-sales service:
Choosing products of well-known brands usually guarantees high performance and quality, and also provides good after-sales service and technical support.
Common brands and models:
Retsch (Germany):
Retsch is an internationally renowned supplier of laboratory equipment, and its disk mills such as the RS 200 and RM 200 series are widely used in many laboratories for their efficient milling performance and stable quality.
Fritsch (Germany):
Fritsch's Pulverisette series of disk mills are widely used worldwide and its equipment provides precise particle size control.
Herzog (Germany):
Herzog offers disc milling equipment designed for laboratory use, widely used in metallurgy, mining and other industries.
Shimadzu (Japan):
Shimadzu's pulverizers are known for their high performance and stability for a variety of laboratory pulverizing needs.
Summary:
Laboratory disc pulverizer is an efficient, precise and easy-to-operate pulverizing equipment for grinding and crushing various materials, widely used in experimental research in the fields of minerals, chemistry, building materials, environmental protection and so on. According to the specific experimental needs, choose the right equipment to ensure the accuracy and efficiency of the experiment.
Main Features:
Working Principle:
The laboratory disk pulverizer consists of a pair of parallel rotating disks. The material is fed into the two discs through the inlet, and is gradually crushed by shearing, extrusion and friction between the two discs.
After crushing, the small particles will be discharged from the discharge port. You can adjust the gap between the discs to adjust the granularity of the crushed material.
Structural design:
Discs: usually made of wear-resistant alloy steel, carbide or ceramic materials to ensure wear resistance in long-term use.
Transmission system: the disc is driven to rotate by electric motor, and the driving method can be realized by belt, gear or direct drive.
Feeding and discharging port: The material enters the crushing chamber through the feeding port, and is discharged through the discharging port after crushing.
Adjustment mechanism: the gap between the discs can be adjusted to accurately control the granularity of the crushing.
Particle size adjustment:
Laboratory disk pulverizer can precisely adjust the granularity after crushing, applicable to different experimental needs. The coarseness and fineness of the particles can usually be controlled by adjusting the distance between the disks or adjusting the rotational speed.
Efficiency and fineness:
Disc Pulverizers are capable of providing high pulverizing efficiency and grinding to finer particle sizes. Common particle sizes typically range from a few microns to a few millimeters, depending on the nature of the material and the equipment setup.
Simple to operate and easy to clean:
Compared to some other complex pulverizing equipment, disc mills are simpler in structure and intuitive to operate. It is also easier to clean and maintain, making it especially suitable for laboratories that require frequent material changes.
Main Applications:
Mineralogical and metallurgical research:
Laboratory disc pulverizers are commonly used for preliminary crushing and grinding of ore samples, especially in mineral sorting, mineral analysis, and particle size control of ores.
Chemical & Pharmaceutical Industry:
Many chemical reactions or the synthesis of pharmaceuticals require fine crushing of raw materials, disc pulverizers are able to handle raw materials of different natures and meet the demand for high-precision particle size control.
Building Material Industry:
Used for crushing raw materials such as cement, gypsum, lime, construction sand, etc., especially in laboratory tests often need to grind different types of particles.
Environmental protection industry:
In the fields of solid waste treatment and waste recycling, disc pulverizers can efficiently crush and grind different types of waste and recycled materials for further processing and utilization.
Material Science and Powder Research:
Used for material powder research, especially experiments involving particle morphology, particle size distribution, and fluidity of materials.
Factors to consider when choosing a laboratory disk pulverizer:
Material Characteristics:
Different materials (e.g. ores, plastics, metals, etc.) may require different pulverizing equipment. Selection needs to ensure that the pulverizer is suitable to handle the hardness, toughness and moisture content of the target material.
Particle size control requirements:
If the experiment requires very fine granularity after crushing, you need to choose a wide range of adjustable particle size, high precision operation of the equipment.
Processing capacity and efficiency:
According to the actual needs of the laboratory to choose the right type of pulverizer, to ensure that the equipment can be in the right time to deal with enough material.
Equipment durability and maintenance costs:
The material of the equipment, wear resistance and the convenience of cleaning and maintenance are the key factors to consider when purchasing.
Brand and after-sales service:
Choosing products of well-known brands usually guarantees high performance and quality, and also provides good after-sales service and technical support.
Common brands and models:
Retsch (Germany):
Retsch is an internationally renowned supplier of laboratory equipment, and its disk mills such as the RS 200 and RM 200 series are widely used in many laboratories for their efficient milling performance and stable quality.
Fritsch (Germany):
Fritsch's Pulverisette series of disk mills are widely used worldwide and its equipment provides precise particle size control.
Herzog (Germany):
Herzog offers disc milling equipment designed for laboratory use, widely used in metallurgy, mining and other industries.
Shimadzu (Japan):
Shimadzu's pulverizers are known for their high performance and stability for a variety of laboratory pulverizing needs.
Summary:
Laboratory disc pulverizer is an efficient, precise and easy-to-operate pulverizing equipment for grinding and crushing various materials, widely used in experimental research in the fields of minerals, chemistry, building materials, environmental protection and so on. According to the specific experimental needs, choose the right equipment to ensure the accuracy and efficiency of the experiment.
Parts List